the refining process
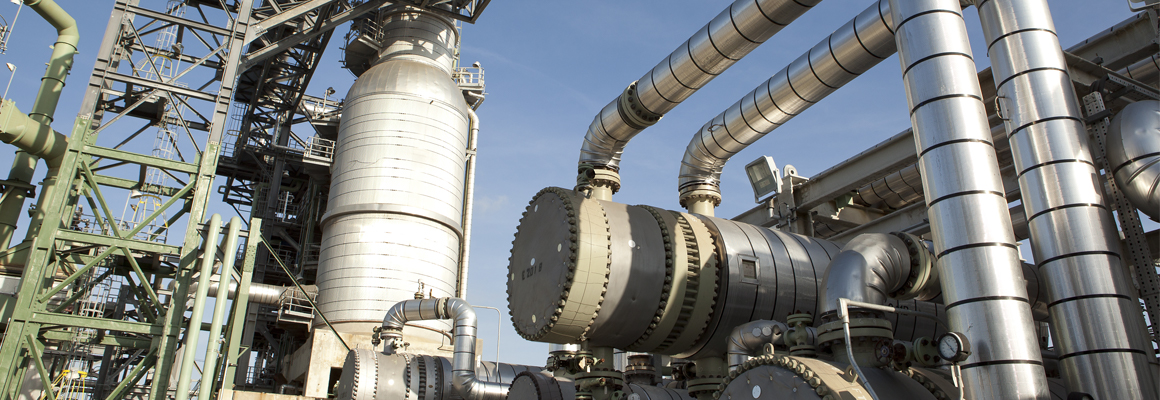
Chevron El Segundo is committed to producing the finest fuels through its refining process. Whether pumped through pipelines or shipped thousands of miles in tankers, crude oil arrives at our refinery in its rawest form.
It is the job of the people who work here to convert that crude oil into fuel we can use – gasoline for cars, jet fuel for airplanes, diesel for trucks and trains, propane and butane for home heating and barbecues, and fuel oils, coke, and certain chemicals for industrial use.
The refining process starts in the distillation towers. Here, liquids and vapors are separated into components according to weight and boiling point. The lighter, more valuable fuels are separated from the heavier products. From the crude units, nearly all of the products are then treated to remove sulfur and nitrogen, primarily by “hydrotreating.” Hydrotreating uses hydrogen to bind with sulfur and nitrogen.
The resulting sulfur is recovered and sold for industrial uses. The nitrogen is converted to ammonia for sale to the fertilizer industry and for use in the refinery. The remaining nitrogen is converted back to harmless nitrogen gas, which is a key component of the air we breathe. The carbon dioxide we recover is sold for uses such as beverage carbonation.
Only about 40 percent of crude oil is comprised of the ingredients for the high-quality fuels we produce. The remaining components of crude are heavy, poor performing fuels. To convert the heavy fuels to usable transportation fuels requires a relatively new process known as conversion or cracking. Using cracking units, the large molecules in heavy fuels are converted into smaller molecules, which we can use to make the transportation fuels you need.
The Chevron El Segundo Refinery supplies 20 percent of all motor vehicle fuels and 40 percent of the jet fuel consumed in Southern California. In order to make these products, we have three main types of cracking units:
- The Coker is a thermal cracking unit. It heats the heaviest portion of the crude to a high temperature, causing it to crack into lighter materials. The light materials produced are gasoline, jet fuel and diesel. The light fuels boil off, leaving behind a solid coal-like material called petroleum coke. Petroleum coke is transported to the Port of Los Angeles, where it is shipped to Asia and Europe to be used in heating and manufacturing.
- The Fluidized Catalytic Cracking Unit (FCC), or “cat cracker,” cracks the heavy material into gasoline, the most demanded transportation fuel.
- The Hydrocracking Unit is another catalytic cracking unit. Chevron’s patented hydrocracking process is called an ISOMAX Unit. The catalyst in the ISOMAX is designed to crack heavy material into jet fuel.
After the molecules have been cracked, these fuels are still not ready to power an automobile or jet engine. The molecules must be arranged and rearranged to burn cleanly and with better performance. The Catalytic Reforming and Alkylation processes all result in higher octane fuels which are designed to meet these needs.
Finally, after more than 200 hydrocarbons and additives have been blended into the fuel, the finished products are held in storage tanks, ready to be shipped via tanker, truck or pipeline to our customers.